Conveyor and automatic guided vehicle
Conveyor and automatic guided vehicle logistics systems and solutions notably increase productivity, eliminating labour constraints and maintaining the rhythm and flows required in the order picking and production processes
At ULMA Handling Systems, we offer a wide range of conveyor and automatic guided vehicles, such as VTD, STV, AGV, motorised transport, gravity transport, turning tables, transfers, lifts, motorised curves, etc.
Conveyor and automatic guided vehicles are used fundamentally to cover the needs of transporting loads between various points. Normally, they are used in conjunction with a transport system.
If you need more information about our conveying solutions, do not hesitate to contact us.
Conveying, how are materials transported?
All materials need to be transported between the different processes of a company, from the lorry to the warehouse, from the warehouse to a process, and also between different processes.
This transport can be carried out manually or automatically with very different technologies depending on the nature of the material. It is very different to transport liquids and gases, bulk solids or packaged and/or grouped packages.
We are going to focus here on the technologies used for the automatic transport of packaged packages, boxes and pallets with a group of boxes or packages.
The first classification we are going to make is based on the size and weight of the package and the second on whether the transport is carried out continuously or discontinuously.
Thus, we can analyse the systems for the transport of light loads (up to approximately 100Kg), or pallets (they can be pallets, baskets or packages) of 500Kg, 1000Kg or more.
Transport of light loads
The most frequently used systems for light loads are conveyors or belts. These are usually roller or belt conveyors, as well as modular belts and plastic chains.
Roller conveyors move the load by means of the rotation of the rollers and the friction generated between the roller and the product which makes it move. They can be straight or curved, normally in a horizontal plane and with the purpose of only transporting or also processing the packages or accumulating them.
There are different technologies for this, such as the use of external motors and transmission to each roller or the use of motorised rollers and transmission between rollers.
These systems are complemented with transfers, pushers or diverters to move from one line to another on the same plane, and elevators to move from one plane to another vertically.
Belt conveyors or belts are made up of a closed belt, normally made of PVC, which moves between two rollers, with an upper traction face and a lower return face, and which moves the package located on the traction face. One of the two rollers, or a third roller, is motorised and is the one that generates the traction to the belt.
In order to divert the bundles to another line, it must be done by high-speed injection or pushers. Elevators can be used vertically, although it is also common to use the same inclined belt conveyor, up or down, and to do so continuously.
Similar to the PVC belt is the modular belt, whose principle of operation is similar, but its construction is based on plastic parts linked together like chain links.
There are also straight and curved sections, and they are very suitable for installations where cleaning is required, although the degree of friction is lower than PVC, so inclined belts do not allow such pronounced angles. For level change, there is the Spiralveyor, which is a spiral belt for reducing the area used.
Lastly, mention must be made of the plastic chains, or hinged chains, whose function is identical to the previous one, but which are used in production lines where the package to be transported is small and much lighter.
As for the productivity obtained with roller and belt conveyors, they can range from 1,000-2,000 boxes/hour to 5,000-6,000 boxes/hour, although there are limiting elements which mean that the flows are lower. In addition to the speed, 30 m/min to 90 m/min and even higher, factors such as the stability of the package, its inertia in the case of liquids, the friction coefficient of the material, the shape of the base, flat or ribbed, and the quality of the package must be taken into account.
Pallet conveyors
For pallets conveying, the continuous systems are very similar to those for light loads, but with a design and dimensioning in accordance with their dimensions and weights.
The difference is that the rollers use turning tables instead of curves, due to their complexity of execution, and the transfers are made of chains instead of belts.
Turning tables are elements that pneumatically or electrically rotate a table, normally by 90º, and have a conveyor on this table for loading and unloading.
Belt conveyors are replaced by chain conveyors, all in a horizontal plane, there is no continuous elevation, and the pallet is supported by 2 or 3 chains depending on the weight and the admissible reflection of the pallet itself. If the pallet is of poor quality or if it is preferable not to take risks, a crossbar is placed between the chains, making it a slat conveyor.
The transfers are made of chains and there are chain turntables.
PVC belts and modular belts are not used. The production rates achieved are around 200 pallets/hour, although starters or frequency variators are required and the stability of the load itself must allow for this.
Other continuous conveyor systems
Other continuous conveyors are used in very specific niches for specific problems. For example, overhead conveyors, using a continuous chain, or the so-called power&free, with a double circuit, one for the chain with continuous movement and the other for guiding the trolleys that can be hooked onto or released from the chain from certain positions. In this way, the trolleys can circulate and change circuits, they can stop for an operation, move to a lower speed circuit for assembly, loading or unloading, or accumulate between processes.
These overhead conveyors are used in the textile sector for hanging garments, for e-commerce with bags that can be easily adapted to different product morphologies, in the automotive industry, etc...
A variant of the overhead conveyor is the underground chain conveyor, with a similar working philosophy but with the loads resting on the ground. This is more suitable for pallets and other heavy loads such as paper reels, although it is displaced by other discontinuous systems which avoid the need for civil works to adapt the building, and are much more flexible if a change of circuit is required.
Discontinuous transport systems
In terms of discontinuous systems, although theoretically they are all guided vehicles, in practice a distinction is made between those that require a fixed guidance system and those that do not.
This technology is based on vehicles that carry the load on them and have a point of origin and a point of destination (from-to) and is often similar to the transport of people by bus or taxi. Those that require a fixed guidance system are the transfer carts with rails on the ground, above ground or buried, and which work in line, with the vehicle circulating in two directions, or in a closed loop, which allows more vehicles to be used but which all travel along the route and have several loading/unloading stops.
The electrovias are trolleys that move hanging from a rail located on the ceiling, fixed to it or to columns supported from the ground. Each trolley is autonomous and carries one or more loads. In the case of electrovias, there can be rail changes, so that the vehicle can select one way or another, however, these detours should only be installed if it is clear that they are to be used because it is an added cost and impairs the flow at that point.
All these systems usually work in closed environments where access by operators is prohibited because of the danger involved. Only electrified monorail systems can work in open environments, but only if the speed of the vehicles is very low and the regulations allow it.
Fixed guideway trolley systems usually work with pallets or similar, and their productivity depends on the system, but they can reach 100-200 to 400-500 pallets/hour transported in the most efficient systems.
Automatic guided vehicle (AGV)
Finally, there are the automatic guided vehicle systems, the AGVs or AMRs, which work with a guidance system, but without fixed guides. They are more flexible systems as they can be changed more quickly and at lower cost, more or less intelligent and fast, and although they were initially used for the transport of pallets, recently they have also been applied to boxes and parts.
AGVs, Automated Guided Vehicles, have a navigation system that allows them to move along predetermined circuits. The navigation systems can be magnetoguided or filoguided, by magnetic tags, laserguided, by reading datamatrix tags on the ground, and lately by Slam Lidar based.
The defined circuits can be very varied and have junctions and detours that allow the creation of passing zones, waiting zones, shortcuts and others.
If the AGV detects an obstacle that makes it impossible to continue, it stops and waits for the obstacle to be removed before continuing.
They normally work in open environments, although there are installations in closed environments where the vehicles do not have a sufficiently reliable people detection system for working at the speeds at which they work.
AMRs, Autonomous Mobile Robots, normally work with Slam Lidar based systems. They can also be datamatrix based.
What makes them different from AGVs is that the robot does not work with predefined circuits but, once the origin and destination are known and the environment is known, they calculate the most efficient route to complete the mission. During the journey, they are constantly on the lookout for changes in the environment, and in that case, they automatically recalculate to a new trajectory avoiding the obstacle.
The flows depend to a lesser extent on the speed of the vehicle, and primarily on the distances to be travelled, and these can range from a few metres to crossing a factory from end to end.
In addition, the number of vehicles influences when in zones one vehicle has to wait for the other.
Thus, each vehicle could do from 10-15 pallets/hour to 25-30 pallets/hour.
Evolution of conveyor systems
In short, the systems described above make it possible to automate the movement of goods within the factory and to fulfil its mission more efficiently:
To move goods within the company in the most efficient way by linking origins and destinations, and fulfilling the required production.
Although continuous systems have a superior capability in moving production, recently vehicle-based systems are experiencing a boom due to their advantages of flexibility, drastic reduction in set-up and consequent immediacy, reusability for different functions or locations, and standardisation resulting in shorter lead times.
Benefits of automated conveying systems:
Ultimately, the benefits associated with automated conveying are:
- Reduction of internal transport costs in the factory and therefore savings in production or preparation costs.
- Reduction of manpower in handling and increased productivity of operators.
- Increased safety, avoiding numerous accidents caused by manual handling.
- Generate a more coordinated and efficient flow between processes, derived from a limitation of the systems themselves.
- Ensure an association between the physical movement of materials and the logical movement in the management systems.
- Ensure traceability in sensitive products such as food or medicines.

Descrambling
Descrambling guarantees perfect individualisation of the products previously separated by layer
More information
Pallet conveyor
Permits flexible and effective long-distance transport
More information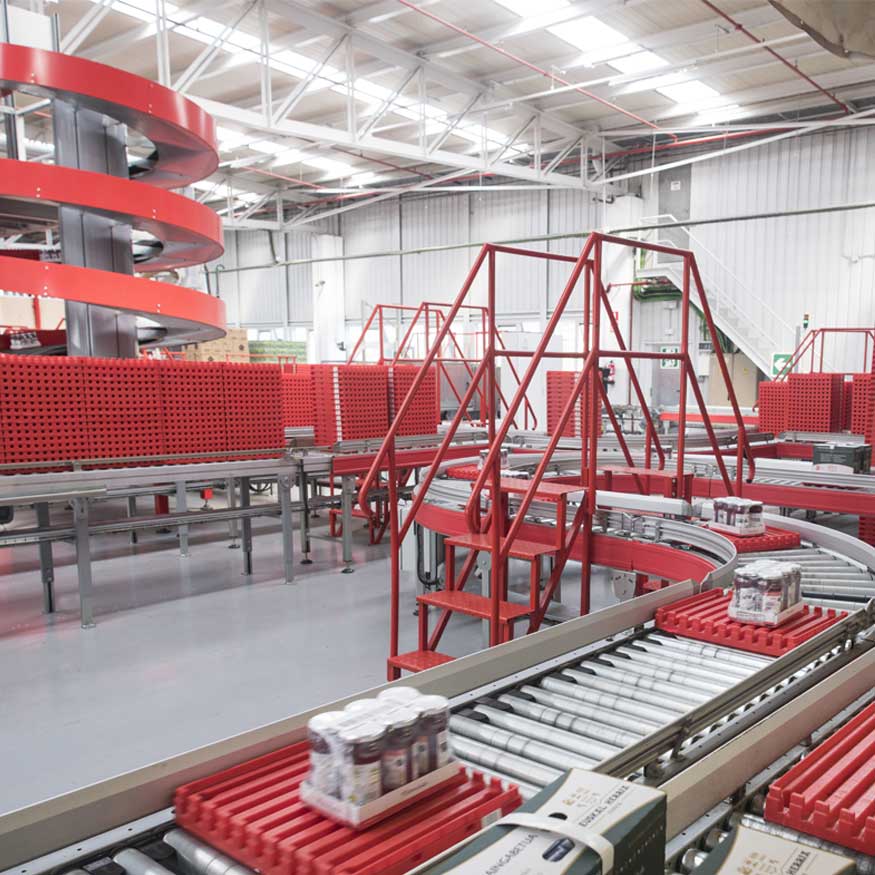
Lightweight load conveyors
Designed to transport products stored in cardboard and/or plastic boxes, containers and trays weighing up to 50kg
More information
Automated Guided Vehicle (AGV)
Fully automated and flexible conveyor and automatic guides vehicle that does not require any human intervention
More information
Sorting Transfer Vehicle (STV)
The Sorting Transfer Vehicle (STV) is a conveyor and automatic guides vehicle system characterised by its reliability and speed, with the capacity to make 800 transfers/hour
More information
Shuttle Carts
Conveyor and automatic guides vehicle with automated transfer control used for moving between motorised stations
More information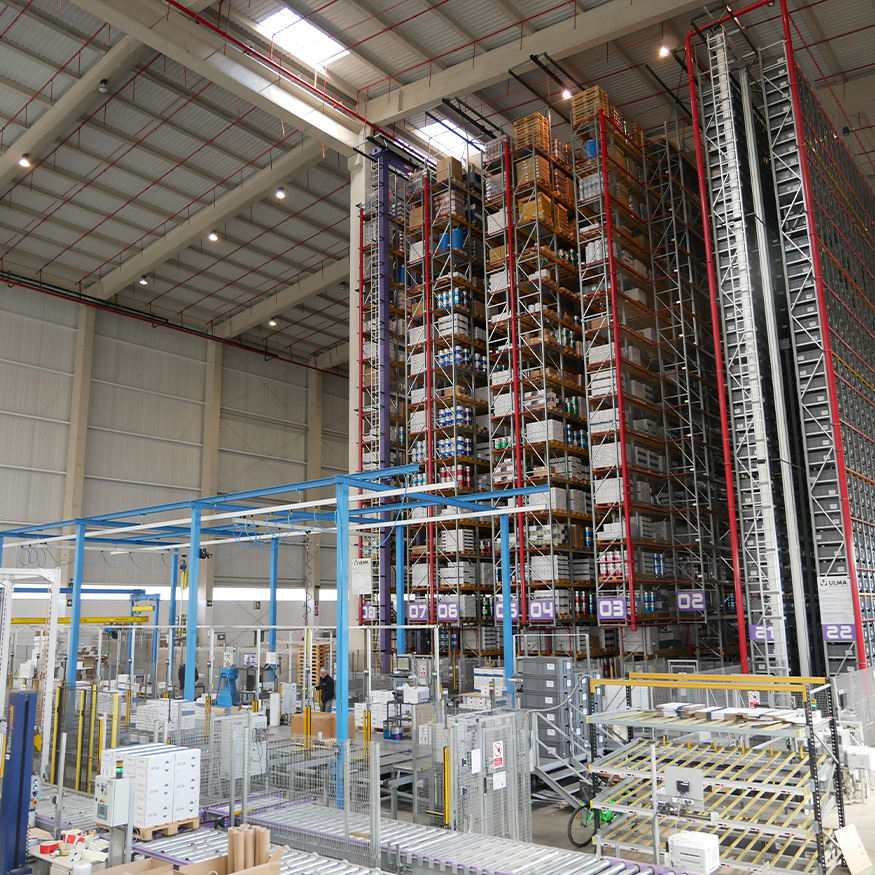
BESA
BESA (Bernardo Ecenarro) opens its doors to automation with ULMA Handling Systems
More information
EROSKI Madrid M50
Groundbreaking fully automatic system for preparing orders
More information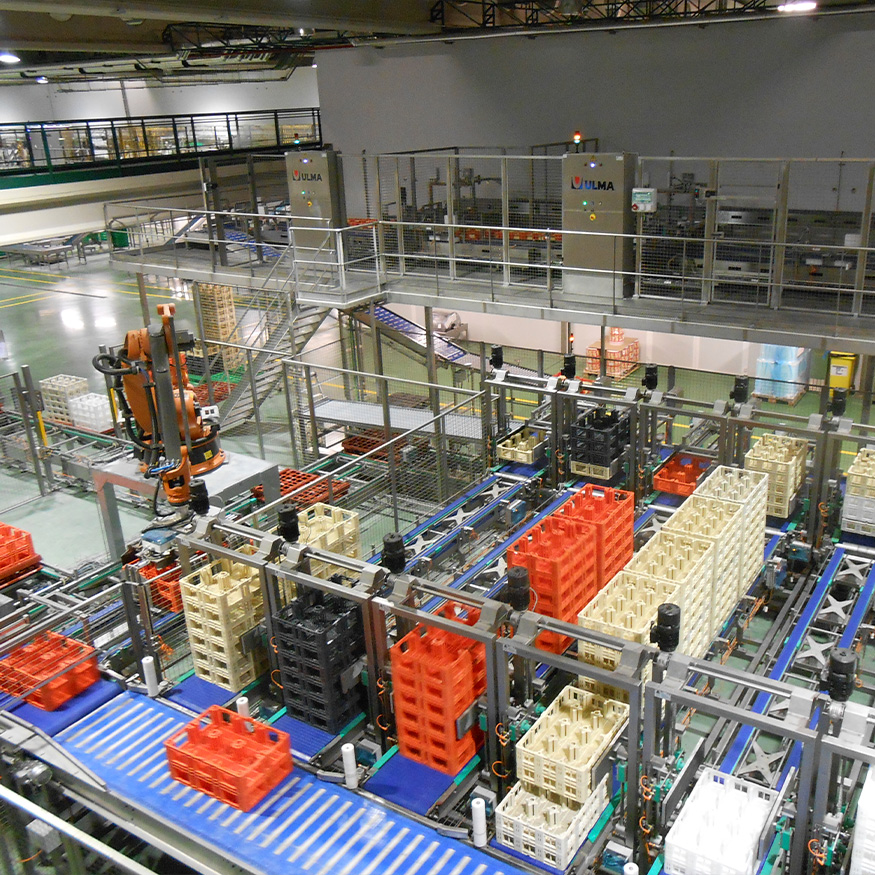
ENTREPINARES
Logistics dedicated to product quality
More information
BONDUELLE
Logistical system at controlled temperatures
More information
SYSTEME U
Logistical optimisation for the French distribution chain SYSTÉME U
More information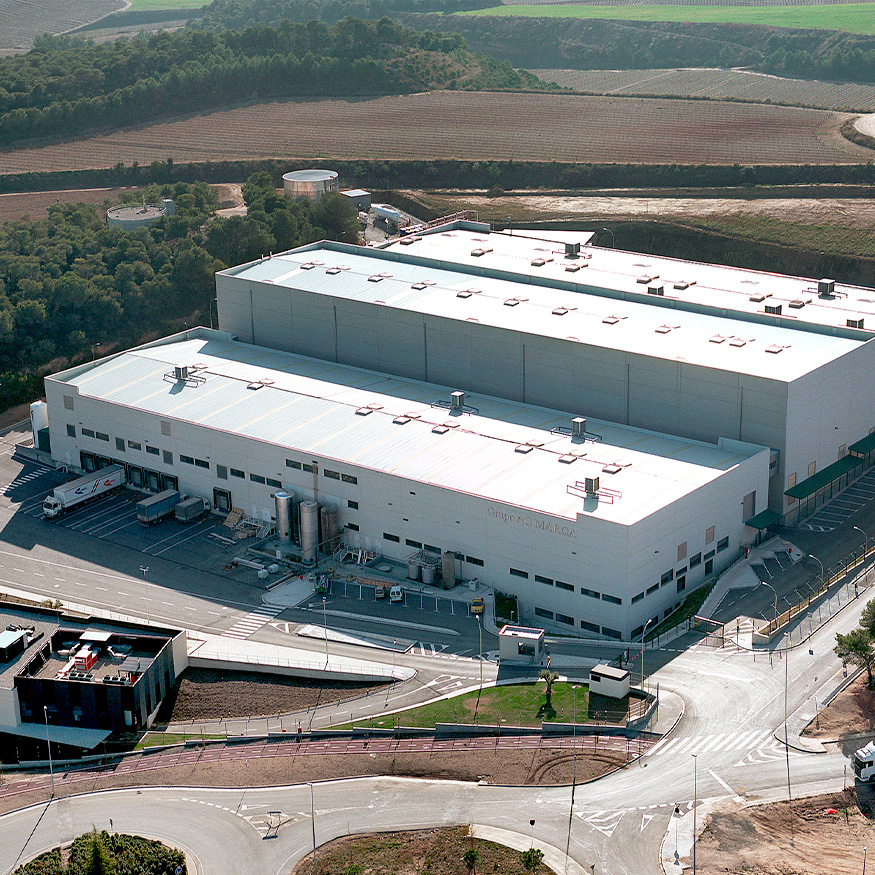
AC MARCA
Automating to increase competitiveness
More informationTalk to us
Do you want to improve your productivity and be more efficient in your logistics?
Request information